Agile only works in software development. This has been my assumption for a long time. Turns out I was completely wrong and non-IT sectors like manufacturing have adapted agile project management and are seeing great results.
Looking for an expert who could give me more insights about agile outside of IT, I reached out to Douwe Attema, a seasoned agile transition coach who has introduced agile project management at numerous engineering companies across Europe and beyond.
The following article is a summary of our discussion. We talked about how agile can be implemented in the engineering and manufacturing sector, what changes are necessary to make it work and what the right steps are to get agile up and running.
Meet Douwe Attema, Agile Transition Coach from the Netherlands
Douwe Attema is an independent agile transition coach with more than 20 years of experience helping companies become more agile, including companies from IT and non-IT environments like automotive, electronics and mechatronics. Douwe holds a Master’s degree in Electrical Engineering and he is also a Certified Scrum Master (CSM). You can get in touch with Douwe via LinkedIn.
Why manufacturers are looking at agile
Many companies in the manufacturing sector are struggling to deliver their projects on time and within budget. While this may be in part due to a lack of project management, the main reason is the increasing technical complexity.
Whether you look at cars, trains, aeroplanes or even washing machines: What used to be purely mechanical systems have become highly complex systems that nowadays include software components, human machine interfaces, electric steering mechanisms, entertainment systems (yep, my washing machine plays Schubert’s “Die Forelle” upon finishing) — there is an almost endless amount of parts and components that go into the final product.
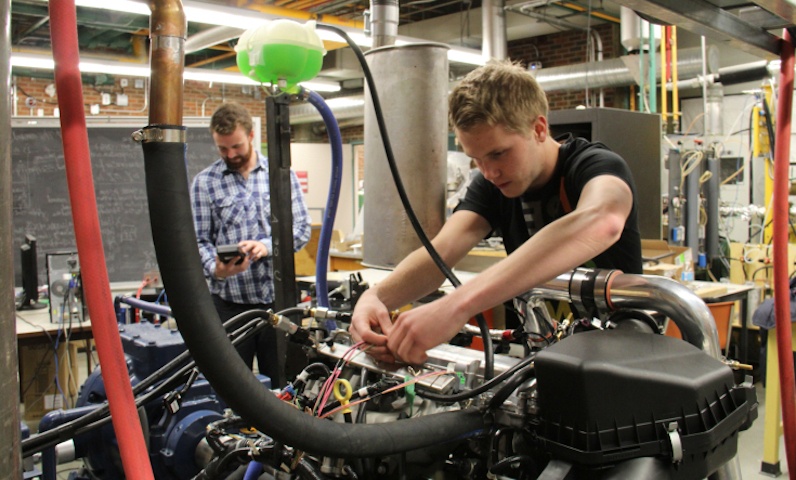
With increased competition and rising customer demands, the product development cycles have also dramatically increased over the past years. The increased technical complexity combined with high market pressure has made it almost impossible for manufacturers to accurately predict product development projects and to give their clients reliable time and cost estimates.
Realizing that their current way of planning and running projects — based on the traditional waterfall model with fixed phases — wasn’t giving them good results, the most forward looking engineering firms started to adapt the agile approach with its typical characteristics:
- less upfront planning
- collaborative teams
- frequent alignment with the client
- an iterative way of working with shorter project cycles (sprints)
- a focus on building a first prototype fast.
Bringing agile into an organization is way more challenging than one might think, and it goes beyond putting up Kanban boards, renaming project phases to sprints and calling the project manager a Scrum Master.
Agile is much more about mindset than it is about the formal side of project management. Therefore, agile can only deliver its full value in companies whose culture is ready for this new way of thinking.
No agile without a change in company culture
How can manufacturers create the kind of culture that is needed for agile?
First and foremost, companies have to let go of what Douwe Attema calls command and control culture: An environment where employees are just executing the plans devised by their superiors, all under tight supervision and control from management.
Instead, companies should give more responsibility and creative freedom to their engineers and other staff members, acknowledging that the employees have the capacity to solve any technical challenge in the best possible way and to come up with great solutions that the customers will like. In the end, this change comes down to trust.
“When you give trust to the people who are actually making the products and you give them the freedom to come up with great ideas and explore the possibilities, this is how you can make product development and manufacturing work in today’s world”
Douwe Attema - Agile Transition Coach Tweet
Since agile companies rely on giving more power and responsibility to employees, this changes also the role of the organization and management: The company and its management become more of a facilitator, making sure that employees have the best tools and knowledge to solve product design and manufacturing challenges.
[sc name=”mediavine-hint”]
How can agile be adapted for engineering?
Agile has been very successful in the software business, but to use it in engineering and manufacturing, some changes are necessary. This was the next topic I discussed with Douwe Attema and he had an interesting story to share.
One of the first non-IT companies where Douwe implemented agile was a company that performed revisions of trains. Clients would come to have their train cars upgraded with the latest technology.
At the outset Douwe was skeptical if agile could be used because until now he had only seen it work in software development. However, Douwe realized that — in many ways — engineering projects resembled software projects. You work on a complex system at the center — in this case a train — and you try to integrate all these complex components and make them work together. In train systems this involved air conditioning, electric wiring, entertainment systems, different materials and so on. Those components had to be integrated just as with software, only that they were physical parts.
So, how were the train upgrading projects organized? For each subsystem such as air conditioning, a dedicated cross-functional team was set up. The team members were the subject matter experts for their respective module. This setup ensured a good level of communication among the experts within a work stream.
For alignment across the technical modules, there had to be some sort of integration where teams could align their activities with the other teams, discuss impediments and see how they could fit all of the pieces of the puzzle together. For this purpose, Douwe introduced weekly cross-team sync meetings which also helped to reduce the risk of teams following different priorities.
Apart from creating a meeting structure that fit the needs of large engineering projects, Douwe Attema and his team used the same role concept as in classic Scrum (the agile framework). Douwe says:
“Basically all the roles that you find in Scrum such as the product owner, Scrum Master, team members — they are still the same in engineering. So you can apply the same roles to an agile manufacturing project.”
The biggest difference between agile in manufacturing vs. software concerned the actual staffing of the agile roles, specifically the role of the product owner.
Who should be the product owner in engineering projects?
In agile software projects you have a product owner which is represented by one person. The product owner is the link between the business side (i.e. the customer) and the technical side which is doing the implementation, and one of his main responsibilities is to determine the product requirements and reconcile with the technical folks.
In software projects, product ownership can be handled by a single person. In engineering projects however, the sheer complexity and size of the involved systems made it impossible for a single person to oversee the product needs.
Douwe Attema came up with a clever but an unconventional approach — distributing product ownership over several people:
- Firstly, there had to be a project manager who was overseeing the entire project from an organizational and management perspective. Someone to set up the overall schedule and project structure, manage stakeholders and the teams and facilitate collaboration and communication.
- Secondly, there also had to be a leader who was overseeing the project from a product perspective. A person capable of making product decisions who understood what features a first product version should include. This person, as Douwe emphasizes, is ideally coming from marketing, because eventually it was the marketing team who had to bring the product to the market.
- Third, with the technical complexity and the necessary integration of components, there had to be a technical person in the “product owner team”. Someone with formal authority who was also widely respected within the organization. Douwe’s choice fell on the head of engineering.
These three people, a marketing expert, the head of engineering and a project leader, form the product owner when agile is used in engineering.
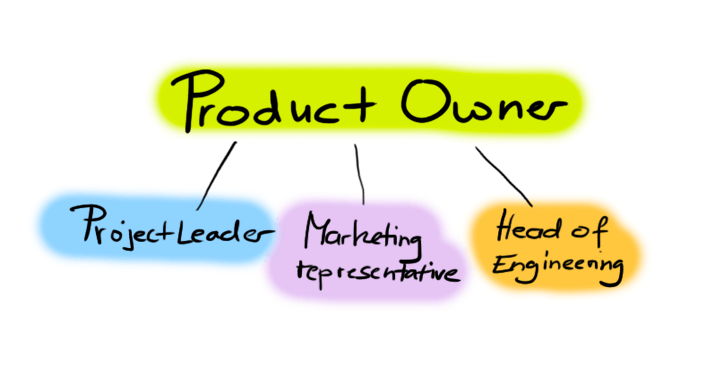
The trio represents the demand side and it has to work together in a democratic way. They set the priorities and define the product requirements, and they are always available for clarifications with the technical teams who are implementing the requirements.
Is the described 3-person setup for the product owner role compatible with the agile philosophy? According to Douwe Attema it doesn’t contradict agile literature and nowhere is it stated that the product owner must be filled by one person only.
“There is no rule that says the product owner should be filled by one person only.”
Douwe Attema - Agile Transition Coach Tweet
With the product owner role settled, Douwe went on to see how they could map the other Scrum roles into the engineering environment, in particular the Scrum Master.
[sc name=”mediavine-hint”]
What does the Scrum Master do in an engineering project?
The Scrum Master is the person who coaches the team so that they can work in the most effective way. His tasks involve clearing obstacles, facilitating communication within the team, liaising with the product owner and other stakeholders and protecting the team from outside interruptions (see definition of Scrum Master).
Based on his experience and the situation inside the company, Douwe felt that there was no place for a Scrum Master in this agile engineering project. Why? Douwe reflects: “When you include a Scrum Master, in a lot of ways he is like a sort of boss in the team. What I have learned is that you don’t want to have a boss in the team. Instead you want to have a self-organizing team.”
As a substitute to the Scrum Master, the role of an agile coach was added to the project. The coach would split his time 50/50 between the teams and the product owner and other stakeholders.
This setup turned out to be the right choice. After 3 months of initial guidance by the coach, the product teams were collaborating very well and the project was moving along fast turning out great results.
“In an agile engineering project, the customer has a voice throughout the project and he is getting helpful feedback at an early stage and not just at the end as in a waterfall project”
Douwe Attema - Agile Transition Coach Tweet
What was the biggest effect of using agile in the train engineering project? Important decisions could be made much faster and the engineering teams could show first results much earlier in the process.
Instead of locking themselves into their offices for 6 months and then showing the customer their results (as in waterfall-driven projects) the product teams were talking to the client on a regular basis to present ideas or to clarify requirements and iteratively work on the final solution.
How agile transforms the product development process
The agile approach in manufacturing doesn’t only influence the way projects are done. It also changes the process of how companies can bring new features to the market.
In traditional manufacturing, product innovation cycles were pretty long. Take the car industry as an example, where new models were released only once every 3-4 years. This slow pace doesn’t work in today’s highly competitive environment where customers are expecting frequent product upgrades (think of smartphones!).
With the help of agile project management, manufacturers are able to speed up their time to market for new product versions without sacrificing quality. Instead of setting up dedicated projects for every product release, engineering firms just have to establish a product development project once.
Then, every new product version is simply an agile iteration through the previously setup project where the self-organizing and cross-functional teams try to incorporate the latest feature requests into the product.
How manufacturers can get started with agile
My interview partner for this article, agile transition coach Douwe Attema, has a long track record of bringing agile into non-IT businesses. So I was curious to learn what process he followed. Manufacturing and engineering is a very conservative industry and getting people to adapt a new way of doing projects presumably is quite a challenge.
Douwe laid out his process for me:
Step 1: Discuss pain points and expectations with management
In a first step, the agile coaches will have an honest discussion with top management where the experts try to get an understanding of the company’s biggest project issues. It may be frequent cost overruns, product rollout or product quality issues that keep the CEO up at night. Whatever it may be — Douwe and team will see how the challenges relate to the way projects are executed at the company.
Step 2: Meet the team
In a separate meeting, the agile coaches will lend their ears to the project team members — the engineers, designers, technicians, marketing people and others — to get their perspective on the current project woes.
Because the agile approach favors team empowerment and leveraging the knowledge and creativity of the team, one of the central questions Douwe wants the employees to answer is: What kind of leadership do you need to make this project successful? The answers to this question usually bring a lot of great ideas to the surface that already make the company’s projects more robust and successful. Usually, it is three things that teams need for great performance: trust from management, early feedback from the client and knowing what direction to take.
Step 3: Choose a pilot project
Talking about agile is easy. Committing to actually following this approach in projects is much harder. To make the transition as simple as possible, Douwe and his team will help the customer to try out agile on a pilot project.
It doesn’t have to be the biggest project, but as Douwe recommends “there should be a little bit of risk in it”, meaning the project should be important enough that people are invested. In a one day workshop the team will simulate the project activities, led by the agile coaches.
At the end of the day, the team will share their impressions from the agile process and give feedback. The goal of the coaches is to show that the agile method does work in engineering environments.
Step 4: Make a decision
After a company has tried out the agile approach on a pilot project, its management has to take the call if they want to switch their entire projects to agile or not. The coaches ask: “What is holding us back from introducing the agile way of working in all our projects?”
After seeing first hand that agile works in their projects as well, the company management usually wants to adapt agile as the new standard. Douwe Attema states:
“After seeing the results from the agile workshop, in 99% of cases the management will say yes let’s do it!”
After the decision has been made, Douwe usually stays directly with the company to get the agile processes up and running and help team members get comfortable with the new way of working.
Douwe will also help the business build up team members as agile coaches so that the company has all the knowledge and skills in house and doesn’t have to rely on external help.
[sc name=”mediavine-hint”]
Conclusion
Agile not only works in engineering. It has become the new way for manufacturing companies who want to secure their economic future. The agile way of working is giving engineering firms a new, powerful tool for handling the technical and organizational complexities in projects as well as the fast-paced product cycles by empowering employees, building self-organizing teams and following an iterative, feedback-driven approach where the customer always has a voice.
Manufacturers who want to implement agile in their organization should understand that this isn’t just a methodological change. Agile is a new way of working together which requires a cultural change: A high level of trust in the employees as well as their skills and creativity, self-organizing teams instead of top-down coordination and the willingness to experiment and take calculated risk.
Working with an agile transition coach can make the transformation easier and more effective, because as an independent outsider, the coach will find it easier to uncover organizational issues by working directly with the employees and come up with a suitable project setup that works for the specific company and industry.
Big thanks to Douwe Attema for sharing his experience and insights in this interview. If you need help making your business more agile, you can connect with Douwe on LinkedIn.
Author
-
Hi, I’m Adrian, a Senior Project Manager and the Creator of Tactical Project Manager, where I teach a pragmatic approach to project management. Led large-scale IT and business projects for over 10 years. My goal is to enable you to lead any project with confidence.
View all posts