Launch 5S in your manufacturing plant in only 4 weeks.
The “5S in Manufacturing Launch Kit” contains everything you need to get started.
Are you sure you want to do 5S?
Maybe just 2S?
Or 4S?
Just kidding
It’s just that:
Many times, companies who start 5S in their assembly don’t get beyond 4S
At the maximum.
They fail to deliver on the “5th S”: SUSTAIN
These manufacturers start a 5S campaign with great enthusiasm.
They understand the benefits that 5S can bring to their operation.
But then, after a few months, the drive starts to die off.
They get back to where they started
They fall back into their previous way of working
Shelves start getting cluttered again
On the floor you can find boxes that don’t belong there.
People stop following the organizational system that was built as part of 5S.
That is really unfortunate, because not only did those businesses spend a lot of effort on reviewing and redesigning their workflows and organization, labeling equipment, creating organizational plans ….
What is most sad in my opinion is that:
The team is frustrated and disillusioned after a failed 5S campaign.
It’s like: “I’ve seen this in a Dilbert cartoon. Management comes up with these fancy ideas they’ve read about in business magazines, then they want us to make all those changes … but it never works out ”
But hey!
Thank God your team has you!
You don’t want to waste precious on an initiative that doesn’t work out.
You are sold on the idea behind 5S
You understand the concept
You’ve read books and articles about it
Maybe you have already launched a small 5S campaign at your previous company.
We want to share with you two rules to keep in mind when launching 5S
Rule #1: Start small, scale later
It is tempting to look at pictures of Japanese factories – spotless, well-organized workspaces that run like well-oiled machines – and think: That’s what we want to build.
The thing is:
If you try and tackle a full manufacturing plant or a full warehouse, it’s gonna be too much for the team to look after.
It’s gonna be overwhelming.
Think of it this way:
When launching 5S in your organization for the first time, you are just spreading the idea of 5S.
Your want people to understand the concept.
But more importantly, you want people to embrace the idea and understand its value by feeling how the improvements implemented through 5S have made their work noticeably easier and more efficient.
You really should start with a PILOT.
So in the initial stage, don’t take on too much.
Focus on zoning and separating out your work area.
Zoning it into sections that focus the accountability within a particular section and which ensures that people can carry 5S on.
Learn as you go.
Improve.
Rule #2: Let the team drive your 5S campaign
We have never seen a single successful 5S rollout that was top-down driven
All staff needs to be on board with the philosophy.
That means 5S should always be driven by the team:
The team must “own” the workspace.
They need to make the diagnosis about issues and bottlenecks in current workflows and organization that should be addressed with a 5S campaign.
After the diagnosis has been made, it’s the team’s responsibility to brainstorm solutions and decide what improvements to make and how to make the operation more efficient and remove safety risks.
It’s a no-brainer:
Why would a warehouse or manufacturing worker not want to remove obstacles that disrupt his or her workflow?
5S is for the team’s own benefit.
And that is what you need to convey when launching 5S.
The key to a successful 5S implementation is to let the team drive the initiative.
Of course, not everybody in your organization will be equally motivated to implement 5S.
Some people will be very skeptical about the idea.
Unwilling to make changes, they may even want to see the project fail.
But also:
- some folks in your organization may instantly “get” the idea of 5S and become really excited about it
- They immediately get to work. They’ll review their organization and processes and come up with fantastic ideas on how to make their area more efficient
Those teams become your 5S ambassadors in the plant.
Their work zones become showcase areas that set the standard for the entire plant.
After a while, the other zone owners will be eager to “5S” their areas as well.
They want to keep up with the other teams.
It becomes like a competition.
“How do we get started with 5S?”
We assume that – as you found this page – you are excited about 5S, you are conceived it will work and benefit your operation.
Because 5S can seem quite complex at the beginning and there are thousands of rabbit holes you could go down and things you could do, we have created specific material to help you get started.
As you are getting ready with 5S, you probably have a few questions:
What prep work is needed for our 5S campaign?
What checklist should I use that will guide us?
How do I get my team onboard?
We can help you!
Because 5S can seem quite complex at the beginning and there are thousands of rabbit holes you could go down and things you could do, we have created specific material to help you get started.
We call it the “5S in Manufacturing Launch Kit”.
The Launch Kit breaks down the process for launching 5S in a manufacturing environment to the essential steps.
The 5S in Manufacturing Launch Kit:
Launch 5S in your manufacturing plant in only 4 weeks
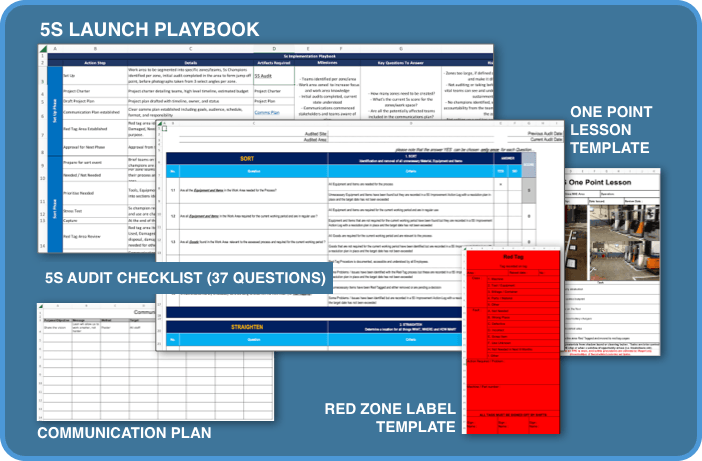
The 5S in Manufacturing Launch Kit is a set of materials to help you rapidly launch 5S in your manufacturing plant. It’s a playbook with the essential steps which keeps you focused on the right track where you can achieve tangible results fast.
The Launch Kit contains the following documents:
- The 5S Launch Playbook outlines the process from initiation to implementation of Sort, Straighten, Standardize, Shine and Sustain actions.
- The 5S Audit Checklist with 37 questions for each of the activity groups Sort, Straighten, Standardize, Shine and Sustain.
- We also included a Red Zone label template for printout. Use the Red Zone label to tag items to be reviewed and sorted first – things like cables, tools, boxes, binders and other times found in a work zone they don’t belong in and for which the correct place needs to be determined first.
- The One Point Lesson Template is used to share solutions around organizational issues discovered as part of the 5S rollout.
- Finally, you’ll also find a Communication Plan Template in the Launch Kit that is used to define a meeting schedule and a schedule for email updates.
Documents included:
This is the document you start with when working with the Launch Kit. The Playbook gives you the “big picture” for your 5S campaign: what you need to do first, second, third and so on. This way you have a systematic process to follow and you are not getting lost with any of the details.
The Playbook also provides you with the following information:
- Required documents: Documentation and artifacts that need to be prepared for each step
- Responsible: Who is in charge of each step?
- Milestones: What should be the outcome within each activity
- Key question:The critical questions to focus on at each stage
- Risks: Potential pitfalls you should be aware of
The 5S Audit Checklist is the core document to guide you through your 5S campaign. It provides you with the key questions to go through in order to review your current workflows and organizational setup and implement suitable improvements.
Questions are arranged according to the 5 stages: Sort, Straighten, Standardize, Shine and Sustain
You can track your progress directly in the Excel-based checklist.
Use the Red Zone label to tag items that need to be reviewed and sorted first – things like cables, tools, boxes, binders and other times found across the manufacturing area at places where they don’t belong at and for which the correct place needs to be determined first.
Meet Daniel Stock, Operational Excellence Expert
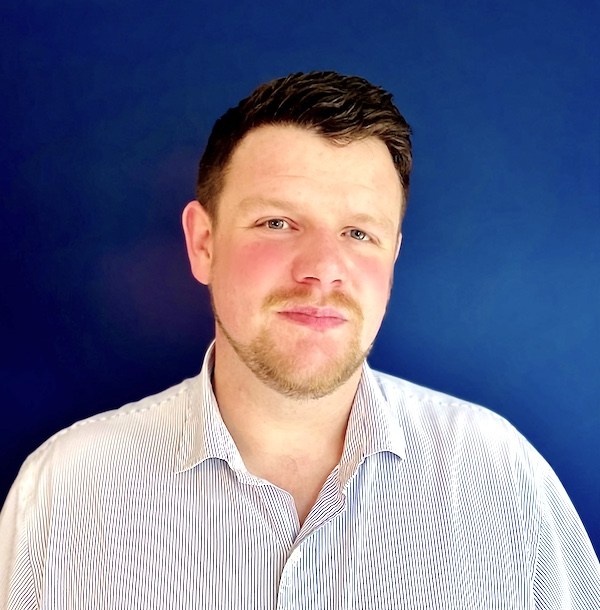
Daniel Stock is a Senior Continuous Improvement and Lean Specialist from the UK, and he is the father of the 5S Launch Kit that you can find here. Daniel has led numerous continuous improvement and manufacturing excellence initiatives for well-known companies including global deployments. Daniel follows a highly pragmatic and people-driven approach to 5S, enabling him to foster a culture of continuous improvement inside an organization, which ultimately leads to lasting and measurable benefits for the company.
If you are looking for assistance with getting your 5S campaign launched, I highly recommend you talk to Daniel. Just leave a message and I’ll put you in touch with Daniel.
Look at the incredible results you could achieve 4 weeks from now (your CEO didn’t believe THIS to be possible)
No doubt, implementing 5S is far from easy.
But the rewards an implementation can bring to a manufacturing plant are simply too great to hold back with a rollout.
Let us show you real examples of improvements achieved within 5S rollouts:
TURN AN AGED PLANT INTO A SHINING AND MODERN WORKSPACE!
When it comes to starting 5S, most of the time we just think of raising efficiency and improving safety.
We forget to talk about the qualitative benefits 5S can bring to a manufacturing plant.
5S can transform an aged and uninspiring facility into an exciting and modern workspace:
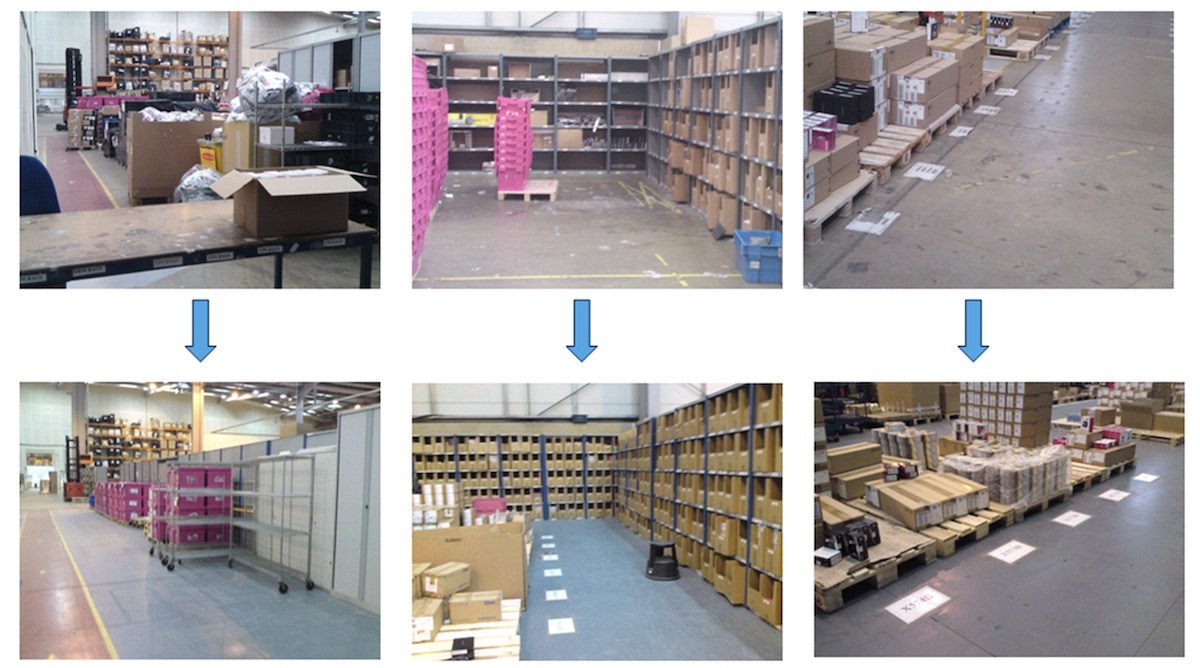
Look at the after pictures (2nd row above):
As an employee, which place would you want to work in?
As a customer, where would you like to buy your goods from?
Maybe you would think: ‘If these guys were responsible for doing something for my business, would they really do it effectively or would they be creating waves in my business by handing it to them?’
Imagine the CEO came over for an unannounced visit and you were selected to show him around. What environment would you like the CEO to see?
It’s obvious.
And all this was achieved mainly with a time investment but no capital investment.
MAKE YOUR PLANT RUN LIKE A CLOCKWORK
Inefficiencies in a manufacturing environment are often hard to detect.
Because everybody has become so accustomed to the workflows
We accept our processes as “standard” because we have always done things that way.
But when you step into the role of an observer and watch the scene for a while, you can tell your operation isn’t running as well as it should be.
Example: Things are getting moved multiple times. Workers unload trailers into a certain area. Then they move it over there to make space for this, then they move this to make space for that. There is this constant budging going on in the warehouse. One pallet gets nudged three or four times before it eventually goes to its processing point.
A 5S campaign can totally transform the manufacturing process by eliminating waste and boosting efficiency.
And it’s actually quite simple:
- Every item gets its own, designated place, and people no longer have to spend hours searching for the tool (or whatever item) they are looking for.
Material used in production is stored in clearly designated zones, with each zone being used only for that particular material and pallet type. There’s no need for support staff to constantly move around boxes or pallets and sort materials.
Your plant could run like clockwork after a 5S rollout.
And when you bring in new staff, they will require less guidance and be able to get settled more quickly because the workspace is well-organized and they know where to find what they need.
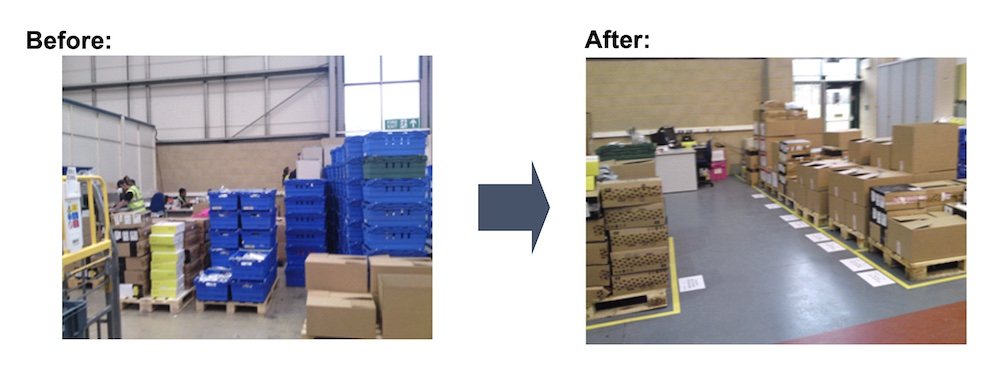
NEVER WORRY ABOUT SAFETY AGAIN
“We are not working safely. We’re going to have an accident at some point because people are putting things everywhere.”
Workplace safety is a BIG concern for management.
And it’s one of the main reasons why management pushes for a 5S campaign.
It’s a lingering fear.
What if an executive came down tomorrow, would you be happy with them walking around and seeing the plant?
Here’s how 5S comes into play:
With 5S, you’re effectively enforcing not only an organized workspace but a safe workplace because things are where they should be. In other words:
An organized workspace means you’ve got a safe workplace!
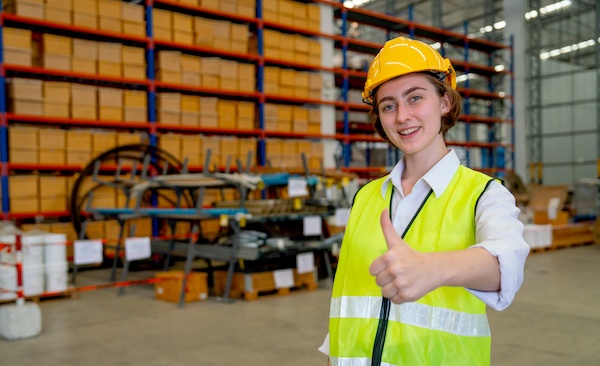
Get the 5S in Manufacturing Launch Kit
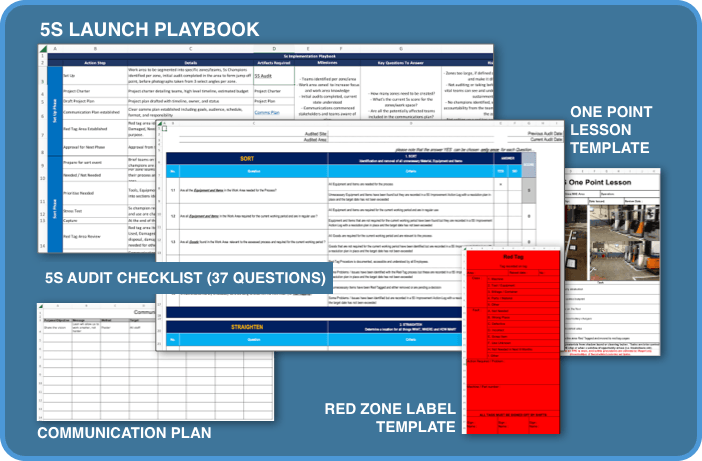
- Created by an Operations Excellence Specialist with extensive experience in implementing 5S and delivering long-term operational improvements.
- You’ll get the following documents:
- 5S Launch Playbook (incl. practical implementation tips)
- 5S Audit Checklist (37 questions)
- One Point Lesson Template
- Communication Plan Template
- Red Tag Label
- Delivered as a set of Excel files
- 30-day-money-back guarantee if you are not happy
- Secure payment via FastSpring, a US payment services provider
- You will get an email with a download link
- Contact form for questions and support